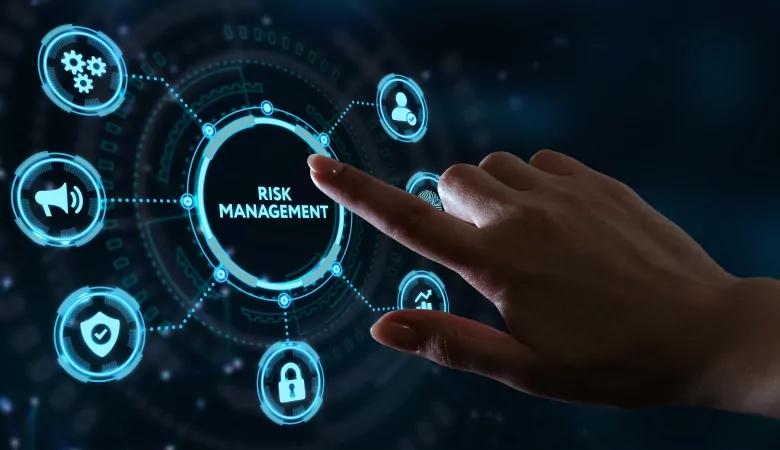
A few years back, supply chain risk was a term used only in the business world. However, it’s currently one of the most discussed subjects worldwide. The pandemic revealed the level of vulnerability that many businesses’ supply chains represented, acting as a catalyst. These days, businesses’ top priority is streamlining their supply chains as they get over the disruptions brought on by COVID-19.
A recent survey indicates that 57% of businesses think supply chain management offers them a competitive advantage. Therefore, any problems with this system could render the company’s operations unviable.
Organisations can seek assistance from supply chain consulting firms to reduce risks associated with supply chain management in various nations. In order to promote smooth management and lower the likelihood of malfunctions, they assist with market analysis and offer suggestions for inventory and administrative optimisation.
Types of Risks in Supply Chain Management
There are now various sorts of risks that can arise in supply chain management. Among the typical ones are:
1.Risk to Finance:
Financial risk is one of the largest supply chain hazards that multinational corporations may encounter. A number of things can cause them, including shortages in the supply chain, unforeseen demand, negative fluctuations in exchange rates, overspending on the budget, and more.
2.Legal Difficulties:
Legal complications typically pertain to matters such as misappropriation of intellectual property, misunderstanding of contractual obligations, failure to comply with terms and conditions, etc.
3.Risks of Inflation:
Unpredictable price increases for goods and services can result from high rates of inflation. Consequently, the price of energy and raw materials needed to manufacture goods rises as well.
4. Shortages of both products and raw materials
According to a recent SAP survey, nearly two out of three companies (64%) are storing more inventory “just in case” to help offset shortages caused by volatile supply. ZF Friedrichshafen AG, for example, was able to “improve availabilities and reduce inventories” within its multi-echelon supply chain management and fulfil its responsibility as a dependable supplier of cutting-edge technologies to the automotive industry by adopting a more comprehensive demand planning approach
5. A lack of clarity
There is a distinction between supply chain management transparency and visibility. An internal advantage of having good visibility is being able to see your operations from beginning to end in real time from a single platform. On the other hand, transparency describes how your business appears from the outside and how willing you are to share your practises. As an illustration, consider the ethical standards of your labour and sourcing practises, as well as the origin of your goods and raw materials. In a supply chain, this is where visibility and transparency come together again because complete transparency is practically hard to achieve without end-to-end visibility.
6.Risk of Natural Disasters
Natural catastrophes such as earthquakes, tsunamis, and floods can happen without warning at any time. Such incidents have the potential to disrupt the entire supply chain by causing harm to people or property.
7.Hazard to the Environment
Suppliers or contractors may pollute the environment during the raw material sourcing process by emitting pollutants, releasing waste, or both. These come under the category of environmental risks and have the potential to result in unanticipated mishaps that harm a company’s brand and bottom line.
8. Dangers from cyberspace
Although cloud-connected supply chain management have many advantages, the growth of IoT networks and connected assets and devices also carries a higher risk. Such systems can serve as extra entry points for potential hackers, so in order to reduce these risks, it’s a good idea to select software solutions with strong cybersecurity built in
5 Best Strategies to Mitigate Risk in Supply Chain
Industry experts estimate that a 62% financial loss can result from supply chain disruptions.
Risk analysis is a necessary task for businesses in order to address the diverse supply chain management risks. In order to mitigate risks in a company’s supply chain management , a process known as risk assessment, identification, and assessment must be put in place.
By doing this, businesses can quickly recover from supply chain disruptions and get back to running normally.
Here are some of the best techniques for risk in supply chain management:
1.Apply the PPRR Framework
Of all the risk in supply chain management techniques, the Prevention Preparedness Response Recovery (PPRR) model is the most widely used. It entails being proactive, creating a backup plan, carrying it out to reduce the risk, and then starting up again to restore normalcy.
Companies that use this risk management model will be able to handle supply chain disruptions in a methodical manner.
2.Make use of logistics planning
Having just one supplier can be dangerous for global companies. This is due to the fact that global pandemics, various geopolitical events, and other macroeconomic factors have the potential to disrupt logistics networks. This might stop the supply chain completely, which would shut down the company as a whole
Thus, it is crucial to have a varied supplier network.The others can continue operations until a solution is found in the event that one closes for any reason.
3.Insurance Protection:
According to Tina, “certain aspects of supply chain management risk are covered by insurance, but not all of them are.” “In contrast to interruptions caused by strikes, which are not easily insured, business disruptions resulting from fire at a major supplier may be covered.” An informed insurance partner can help you navigate the complexities and comprehend the ways in which your company can be safeguarded.
4.Establish Cybersecurity Requirements
Determine compliance with cyber security
Given that the majority of businesses operate at least partially online, cyber threats can be quite problematic. Currently, companies have no control over the cybersecurity precautions that their supply chain partners take. Therefore, businesses can set cybersecurity compliance standards to reduce risks.
In order to reduce cyber threats, this will force all supply chain participants to adopt a specific degree of cybersecurity.
5.Boost the agility of the supply chain
When your supply chain is agile, you can respond swiftly to changes in the market, which improves your protection during unplanned disruptions. One of the most important steps in reducing supply chain management risks is to increase supply chain agility.
Among the greatest methods for increasing agility are:
Preparing and establishing reorder points for inventory
tracking current information and regularly generating inventory reports
depending on a distribution strategy for inventories
collaborating with a provider of omnichannel fulfilment
In what ways do consulting firms for supply chain management aid in risk mitigation?
pletheonconsulting and other supply chain management consulting firms offer services that can meet every requirement of a business’s supply chain. Through their vendor development services, businesses can collaborate with reputable suppliers to source goods.
To help their clients’ businesses run as efficiently and profitably as possible, these companies also handle inventory and perform operational analysis. In addition, they provide advisory services for supply chain outsourcing to guarantee uninterrupted operations for businesses.
Supply chain risk management FAQs
Below are answers to the most common questions about supply chain risk management.
Q1.What is supply chain risk management?
At the most fundamental level, supply chain management (SCM) is management of the flow of goods, data, and finances related to a product or service, from the procurement of raw materials to the delivery of the product at its final destination.
Q2.What are the main risks of the supply chain?
growing cost of fuel for air, sea or road freight transportation. The cost of raw materials is rising due to rising commodity prices. increased labour expenses from manufacturers and suppliers. Intricate global logistics resulting in rising expenses for product management, storage, and transportation.
Q3.What is the first step in supply chain risk management?
Finding every event that has the potential to either positively (opportunity) or negatively (risk) impact the project’s goals is the first step in the risk management process. Project benchmarks. Project’s financial trajectory.
Q4.What is the difference between supply chain risk and a supply chain issue?
Whereas a supply chain is at risk of something that could potentially cause problems later on, an issue is something that is already affecting the supply chain.