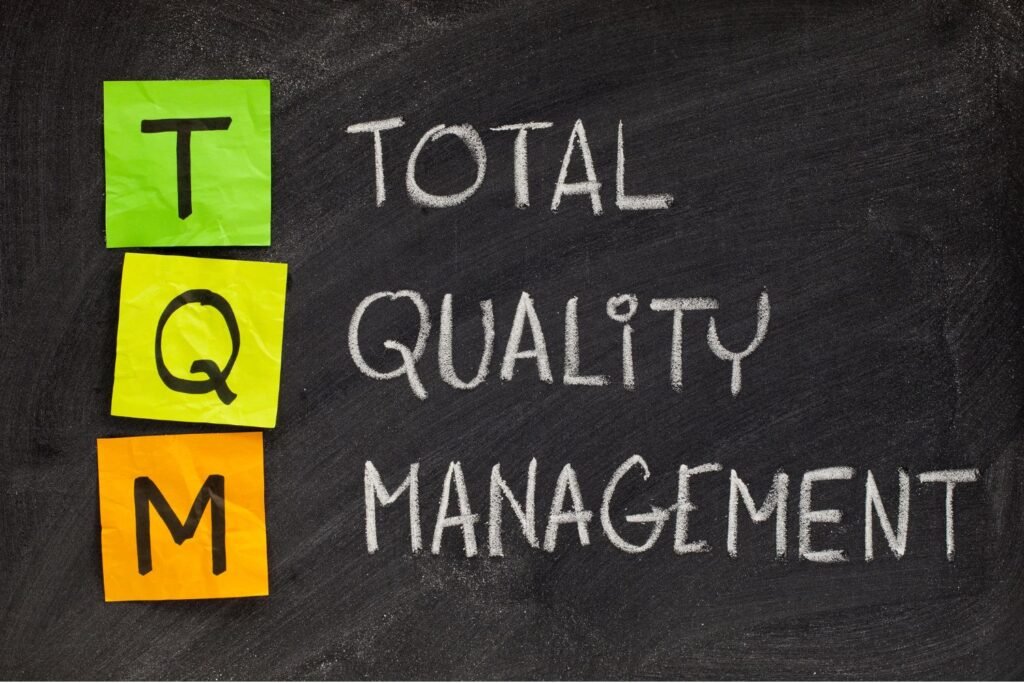
At Plethoen Consulting, our focus is to help businesses grow wiser and more potent. One critical topic we love discussing is Total Quality Management (TQM). Now, you might be asking what Total Quality Management is and why it should concern you. Total quality management is a way of doing business by ensuring that all process and system steps add value. As you can see, it’s not complicated, and the rewards are immense. Let us look at the core advantages of Total Quality Management and how your company could benefit.
1. Higher Quality Products and Services
When it comes to Total Quality Management, the most fundamental is quality. Implementing TQM, an organization puts the focus and effort into providing the best products or services possible. There are fewer mistakes, and customers get what they expect or even more. At Plethoen Consulting, we help businesses refine their processes, meaning every product or service they offer unwaveringly stands behind. No one wants to be uncompromising on quality, and customers appreciate quality-based quality-based services and products, so they will choose you, which is a win for all.
2. More Satisfied Customers
Customers appreciate it when things are running smoothly. With Total Quality Management (TQM), you pay attention to the customer’s voice and meet their requirements each time. Satisfied customers do not just remain with you; they refer their friends and relatives to you. This reinforces loyalty and increases brand equity. At Plethoen Consulting, customer satisfaction is paramount. We assist businesses in effectively using TQM, which enables them to keep their customers and smile.
3. Cost Effective
Mistakes are costly. Fixing misproduced products or redos on unbilled work takes time and money. Total Quality Management TQM enables you to identify potential problems at the onset. If you perform tasks correctly the first time, you will spend less and save much money. At Plethoen Consulting, we teach business owners how TQM helps meet organizational goals with smart budgeting without cutting corners. It’s an effective way to tighten the budget belt.
4. Enhances Team Morale
Total Quality Management is not monotonous; it is diverse and involves people. When people focus on work, they work to ensure that it is done qualitatively. Under TQM, everyone works to share ideas and solve problems collectively. This builds much stronger teams that motivate the team. As one of the leading consulting firms in the United States, Plethoen Consulting enables companies to establish an environment that employees appreciate. Happy teams lead to excellent business outcomes; as we say at Plethoen, the results speak for themselves.
5. Promotes Business Scaling
Positives in products, services, and brand effectiveness lead to satisfied customers, and all of them, when put together, yield business growth. What is the result of using Total Quality Management? An all-around improvement in sales compared to businesses that don’t focus on quality. With proper implementation and analysis of TQM, there will be cleaner workflows. We helped our clients overcome the most complex challenges with strict market competition and come out on top by honing TQM into their business management systems. It’s a secret weapon for growth.
6. Lowers Complaints
Complaints are an inevitable side effect of today’s customer-centric market that many businesses dislike. With more firms implementing Total Quality Management, the area of focus is getting everything done right in the first attempt. This leads to a massive gap in dealing with customer complaints. With less worrying about maintaining trust, our clients gain a more positive perception of their services: more trust means less stress. Many businesses have opted to rely on Plethoen Consulting’s experts and make use of TQM as a vehicle to lower complaints and bolster satisfaction.
7. Better Processes
Total Quality Management encourages people to evaluate how they do things. Are there methodologies that step on the brakes? Is something working better? TQM guides you to finding the answers and improving. As a consultant, Plethoen loves showing companies how to optimize their workflows. Faster processes produce quicker outcomes and enhance the happiness of the teams. Thus, smoother processes equal faster deliverables and result in improved employee satisfaction.
8. Builds a Strong Reputation
Word of mouth about businesses that do fantastic work spreads fast. Using Total Quality Management, the quality of the work becomes your identity. Partners and customers start to regard the company as highly credible and trustworthy. At Plethoen Consulting, we support clients in devising respective business strategies using TQM to build a good name and respect for the people. A positive reputation increases the chances of coming across new business opportunities.
9. Keeps You Ahead of the Game
The pace at which markets are changing is exceptionally rapid. This is why Total Quality Management is critical. Constant improvement ensures that you are always ahead of unadaptable competitors. It’s not about strictly keeping up but being at the top. At Plethoen Consulting, we consult companies on further niches of TQM and how it positions them as leaders in their fields.
Why Choose TQM?
What makes you want to implement a business plan revolving around Total Quality Management? The answer is relatively straightforward- it provides results. TQM integrates quality, collaboration, and cost-effective strategies for your business. Total Quality Management complements anyone from a small startup to a seasoned business magnate. It’s more than a marketing gimmick because it changes people’s attitude: We can always do better.
At Plethoen Consulting, our clients tell us how TQM has improved their companies. The list is long, from better products and enhanced team morale to the benefits. We are pleased to help you make Total Quality Management beneficial for you. Our team is well-versed in methods of Process Improvement and success building. We don’t speak of TQM constructs; we practice them with our clients.”
How to Start with TQM
Would you like to give Total Quality Management a try? It is so much easier than applying cosines the first time. Look at what you are already doing. Where are the areas of improvement? Your staff might have something better to offer, too. At Plethoen Consulting, we walk with you in the implementation and as the process evolves. Not all practices will work for everyone, and we ensure that TQM is implemented in your business to bring results quickly.
Final Thoughts
Total Quality Management (TQM) is revolutionary. It’s about operating efficiently, customer satisfaction, and nurturing growth. The benefits are tangible: improved quality, reduced costs, and a prepared workforce. At Plethoen Consulting, we care about your business’s success through TQM. Need more information? Contact us now. Together, we can achieve greatness.